Chemically Resistant Resin Floor
Chemically resistant resin flooring first requires a clear and comprehensive understanding of the exposure the finished floor is to be subject to and almost by definition; ‘Chemical Resistance’ is a very technical and complex subject.
Chemically resistant flooring system selection, specification and installation firstly requires a clear and comprehensive understanding of the specific chemical resistance requirements for each project, and often the different areas within each project. The key questions are what chemicals are in the area and how are they used and how can they be spilled or otherwise come in to contact with the floor surfaces and details? It is also necessary to know and understand the concentration of these chemicals – Are they used concentrated or diluted, and to what extent, as floor finishes and other materials resistance and consequent durability can vary accordingly, plus if not promptly cleaned-up dilute spillages can become concentrated due to evaporation. This next requires knowledge about the levels of exposure and the frequency / length of exposure time, as well as when and how these will be removed and or rinsed and diluted / cleared-up / cleaned etc.
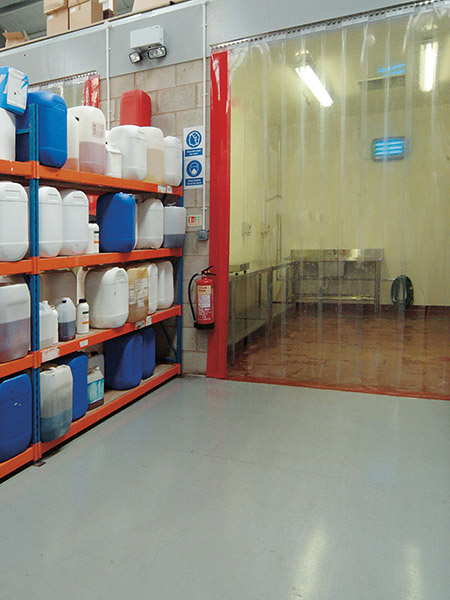
Almost by definition therefore, ‘Chemical Resistance’ is a broad term covering an extremely technical and complex subject. For example, there is a big difference between selecting a floor finish to resist the occasional few drops of a single dilute acid reagent on a laboratory floor, to a finish to resist the sudden spillage of many litres of concentrated acid in a containment zone e.g. due to mechanical failure or accident. Equally there will be a big difference in a resin floor system designed to withstand continuous forklift traffic, broken glass and exposure to the dilute acid on a wet production / processing area floor, to the best resin floor system to resist continuous immersion and exposure to variable mixes and concentrations of the same acid and many other chemicals in secondary containment zones, wastewater collection systems and treatment plants.
History of Chemically Resistant Resin Flooring
Chemical resistance is inherent to resin floors, and these have been used for many years now since their commercial introduction around 60 to 70 years ago, and the technologies involved have also moved on significantly, with continual improvements in the possible performance characteristics of different resin flooring materials. Chemically resistant resin flooring has been used to provide the protective finishes on concrete floor slabs in a wide variety of manufacturing, process, storage and logistics situations to resist the attack and penetration to the concrete structure, or increasingly today, to protect the ground water and the environment, against a huge number of different chemical and combinations thereof – And also at different temperatures whilst under additional stresses such as dynamic loading from vehicles and process equipment for example.
Chemically Resistant Resin Flooring Requirements
In any chemical resistance situation the first requirement is usually that the resin floor is water and liquid-tight, and impermeable to liquids in order to prevent aggressive agents reaching the concrete or the environment below. The second is that the resin floor system itself is sufficiently resistant and its performance is unaffected by repeated or continuous contact with the aggressive chemicals that are present. Obviously to any chemists, but not necessarily to the rest of us mortals, no single type of resin floor or system will be resistant to all of the possible chemicals, their different possible concentrations, combinations and temperatures etc., as mentioned previously. Therefore different types of chemically resistant flooring and floor systems / resin system build-ups will be required for specific project conditions and requirements.
When a high performance resin floor is required and a durable, long-lasting floor finish is to be achieved, then it is important to select the right resin flooring system and its build-up with the component resin flooring products. This must be done carefully and with expert advice – All resin flooring systems are definitely NOT the same. A generic ‘resin floor’ type or generic ‘resin floor system’ specification, such as an ‘epoxy’, or a ‘self-levelling resin floor’, are totally inadequate generic descriptions and specifications, as these can be met by resin flooring materials with vastly different thicknesses, performance characteristics, durability and importantly also – cost as well as their actual chemical resistance!
The requirements for the chemically resistant resin flooring system on any project must be much more specific and detailed, in order to select the right type of resin flooring, the right resin flooring system, the right resin flooring product build-up, plus the right resin floor thickness and detailing solutions for each area of each project.
Check list for Selecting Chemically Resistant Resin Flooring
In order to determine the most appropriate resin flooring system for any given chemical resistance requirements it is necessary to review a number of key factors to make the right selection decision. This should always include a review and consideration of the following criteria before making the final selection. This is because these variations can make considerable and significant changes in the level of aggressive attack that will be imparted on the resin floor, for example from being negligible with dilute concentrations and lower temperatures to having strong and very aggressive oxidising and attack actions at higher concentrations and / or higher temperatures. This review should always be made including consideration of the possible:
- specific chemicals and combinations of chemicals involved (combinations of different acids. nitric and sulphuric for example have a more aggressive effect when combined than they do individually)
- range of concentrations of the chemicals (remembering that spillage of a 2% solution can lead to exposure at 20-20% or more following evaporation on the surface)
- range of combinations
- range of temperatures
- length of exposure (excepting wet areas and continuous immersion requirements, spillages of chemicals should normally be cleaned up as soon as possible for health and safety).
Plus all of the other normal floor system design considerations and especially any other anticipated simultaneous exposure and stresses to which the floor and specifically the resin floor finish will be subjected.
NCC Resin Flooring can guide you and your professional team through this very necessary evaluation process, to ensure that the optimum resin flooring system is selected for your project, including alternatives that may be required for different areas and applications on the same project – process and storage areas, wet and dry exposure, higher and lower temperature environments etc.
Chemical Resistance and Chemical Attack / Deterioration of Resin Floors
A resin floor surface that has broken its polymer structure and components to the extent that it can no longer fulfil its function is obviously not sufficiently resistant when it is being attacked. This may become evident as erosion of the surface, softening or embrittlement leading to early wear, blistering or delamination. Other effects that could include superficial staining, progressive yellowing or some discoloration may not actually result in any loss of the resin flooring systems performance and chemical resistance – in fact it may be part of how this is achieved; therefore this is also not serious so long as the appearance and aesthetics were not also key requirements.
Chemically Resistant Resin Flooring Solutions
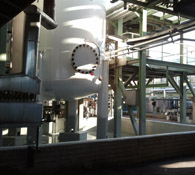
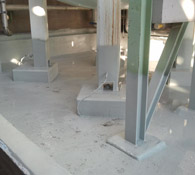
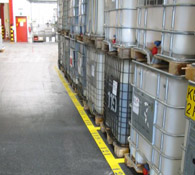
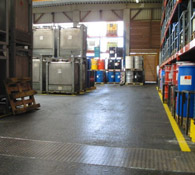
NCC Resin Flooring Site provides complete resin flooring advice and we supply the right resin flooring materials for all of these different areas and applications. We only use the latest resin flooring technologies from the world’s leading resin floor manufacturers – These include the following high performance resin flooring systems: Epoxy and PU resin systems, VIP’s Polyurea and Polyaspartic resin systems and Atako’s ATB-300 highly specialist Vinyl Ester Resin Flooring Systems for extreme chemical resistance against strong acids and oxidising agents, or hydrocarbon solvents for example. It is also very unlikely in modern facilities, simply because of normal health and safety procedures in the event of any accidental spillages or damage that the most aggressive chemicals would be left in contact with the floor for any length of time before they are removed and the surfaces thoroughly neutralised and cleaned off.
As always, NCC Resin Flooring works closely with the industry’s leading chemically resistant floor finishes of all of the different resin and formulation types available to ensure that we can offer fully independent and qualified technical, commercial and practical advice on the best system solution for your project. This is to ensure that our experts can help you to achieve the design, high quality finish and durable floor that you require for your project with the best epoxy, PU, Polyurea or Vinyl ester resin flooring solution, whichever is the most appropriate for your individual situation and requirements. For more information and assistance on your chemically resistant floor project, please call any of our offices and one of our experts will be pleased to assist you.
We hope the information relating to your industry area and project is useful and of initial assistance. You are also welcome to call us for our FREE support at any time on: 01257 266696 Alternatively, you can email us technical@resinflooringsite.co.uk and we will get back to you just as soon as we can.